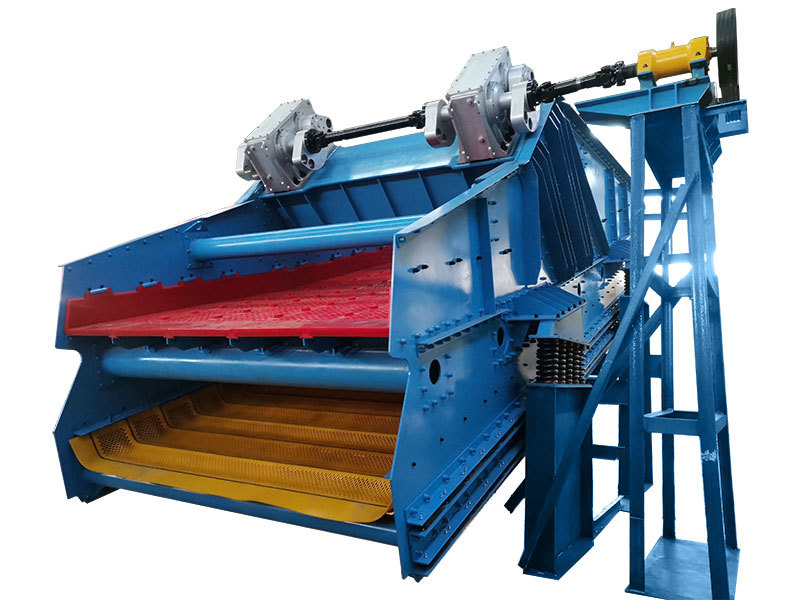
Share to
Flip-Flow Screen
Still deciding? Get samples first, Contact US !
View similar products
Tag list
- Description
-
Since its development in the early 1960s, flip-flow screens have evolved from novel equipment to a mature and reliable solution for screening challenging fine, wet, and adhesive materials. Their core flip-flow motion principle endows them with exceptional anti-blinding capability and high-efficiency screening characteristics. The emergence of diverse structural configurations—including single-deck, double-deck, banana-type, and modular double-deck designs—has further expanded their application scope. This versatility enables flexible adaptation to complex industrial scenarios with varying scales, material properties, and product requirements. Advancements in materials science and smart control technologies will continue to position flip-flow screens as critical components in enhancing resource utilization efficiency, reducing energy consumption, and enabling green production practices.
Working principle
The core working principle of flip-flow screens utilizes a dual-mass vibration system to actuate the elastic screen surface, generating high-frequency, large-amplitude, nonlinear "tension-relaxation" periodic deformation. This enables efficient forced screening of fine-grained, wet, and adhesive materials. Technically, the system fundamentally represents a sophisticated integration of mechanical dynamics and the elasticity of materials.
Core Advantages
The high-frequency, large-amplitude flip-flow motion of the elastic screen surface expands screen apertures to their maximum design opening size, permitting near-mesh particles to enter or pass through. Upon instantaneous contraction (or complete closure) of the apertures, trapped particles undergo intense compressive forces and are subjected to a powerful ejecting action. This mechanism fundamentally resolves the severe aperture blinding inherent in conventional rigid screening equipment when processing wet, adhesive, fine-grained materials. Consequently, flip-flow screens deliver irreplaceable high-efficiency solutions for dry screening of challenging fine, wet, and cohesive materials. This technology demonstrably enhances resource utilization rates, elevates product quality, and optimizes production efficiency.
Application Industries
Coal: Efficient screening of wet and sticky raw coal, washed clean coal, and coal slime with particle sizes <6mm (especially <3mm), solving the severe screen blinding and low efficiency problems of traditional screening machines. Achieves precise control of product top size (e.g., 50mm, 25mm, 13mm, 6mm, 3mm, etc.) to enhance commercial coal quality.
Metal Ores: Fine particle classification of ores; efficient processing of wet, sticky ore fines (<10mm, especially <5mm) such as iron ore, copper ore, gold ore, lead-zinc ore, bauxite, and phosphate rock. Precisely controls feed size for grinding or final product size.
Non-Metal Minerals: Fine classification (down to 0.1mm) of quartz sand, feldspar, kaolin, bentonite, etc. Removes impurities to enhance product purity and added value.
Construction Aggregates & Sand Industry: Fine classification of manufactured sand and crushed stone, especially in humid conditions. Efficiently separates fractions like 0-3mm, 3-5mm, 5-10mm. Controls stone powder content and improves sand quality.
Solid Waste Resources & Environmental Protection: Sorting of industrial slag and recycled resources (e.g., construction waste).
Screening Efficiency:Fine particle classification efficiency >90% (especially for <3mm material), significantly exceeding traditional vibrating screens (typically 60-75%). Critical particle passage rate is substantially improved, effectively resolving the blockage issue of "near-mesh particles". Demonstrates strong adaptability, maintaining high efficiency even with material moisture content reaching 10-15% or higher.
Throughput Capacity: Processing capacity per unit screen area reaches 2-3 times that of traditional vibrating screens (particularly for difficult-to-screen materials).
The Banana-type Flip-flow Screen increases throughput by over 30% within the same footprint through its multi-stage variable-angle design.
Classification Accuracy:Screening precision index (k-value) ≥0.95 (traditional screens: 0.7-0.85), resulting in more concentrated product size distribution. Effective separation cut point as low as 0.1mm meets ultra-fine classification requirements.
Anti-Blinding Capability: Dynamic screen aperture deformation enables self-cleaning, completely eliminating clogging issues with sticky, high-moisture materials.
Modular Design: Facilitates rapid screen media replacement. Compatible with various materials including wire mesh and polyurethane panels to accommodate different material characteristics.
Screen Media Design: Polyurethane panel service life reaches 6-24 months with 5x-10x improved wear resistance. Modular construction allows sectional replacement, reducing maintenance costs by >50%.
Intelligent Control:Optional VFD for vibration frequency adjustment or PLC integration for automated control.
Ø Additional Notes
Customization Service: Customizable screen deck dimensions, number of decks, inclination angle, and materials (e.g., stainless steel, polyurethane) according to requirements.
Technical Specifications Table
Equipment Model Single-layer Screen Area (㎡) Screen Deck Layers Screen Aperture (mm) Feed Particle Size (mm) Processing Capacity (t/h) Power (kW) Vibratory Force (KN) Overall Dimensions (mm) HCZS1548 7.4 1 5-50 ≤100 50-400 18.5 20 5500X3400X3200 2HCZS1548 7.4 2 5-50 ≤100 50-400 22 28 5500X3400X4200 HCZS1848 8.9 1 5-50 ≤100 50-500 22 24 5500X3700X3400 2HCZS1848 8.9 2 5-50 ≤100 50-500 30 32 5500X3700X4400 HCZS1861 11.2 1 5-50 ≤100 50-500 22 28 6700X3700X3400 2HCZS1861 11.2 2 5-50 ≤100 50-500 30 36 6700X3700X4400 HCZS2161 13 1 5-50 ≤100 50-600 30 32 6700X4000X3400 2HCZS2161 13 2 5-50 ≤100 50-600 37 44 6700X4000X4400 HCZS2448 11.9 1 5-50 ≤100 50-700 30 36 5500X4300X3400 2HCZS2448 11.9 2 5-50 ≤100 50-700 45 52 5500X4300X4400 HCZS2461 14.9 1 5-50 ≤100 50-700 37 40 6700X4300X3600 2HCZS2461 14.9 2 5-50 ≤100 50-700 45 56 6700X4300X4600 HCZS2761 16.7 1 5-50 ≤100 100-800 45 56 6700X4700X3600 2HCZS2761 16.7 2 5-50 ≤100 100-800 45 72 6700X4700X4600 HCZS3061 18.6 1 5-50 ≤100 100-1000 45 68 6700X5000X3600 2HCZS3061 18.6 2 5-50 ≤100 100-1000 55 88 6700X5000X4600 HCZS3073 22.3 1 5-50 ≤100 100-1000 45 76 7830X5000X3600 2HCZS3073 22.3 2 5-50 ≤100 100-1000 55 96 7830X5000X4600 HCZS3673 26.8 1 5-50 ≤100 100-1400 55 92 7830X5700X3600 2HCZS3673 26.8 2 5-50 ≤100 100-1400 75 116 7830X5700X4600 HCZS3685 31.3 1 5-50 ≤100 100-1400 75 104 9100X5900X3700 2HCZS3685 31.3 2 5-50 ≤100 100-1400 90 132 9100X5900X4700 For more detailed technical specifications or application cases, feel free to contact us for further discussion!
Next: Shaftless Trommel Screen
Flip-Flow Screen
Still deciding? Get samples first, Contact US !
Products Category
Tag list
Flip-Flow Screen
Inquire Now
Note: Please leave your email address, our professionals will contact you as soon as possible!